Soldering is a common technique commonly used in printed circuit boards to join various metals together to ensure the smooth flow of electricity. The process involves melting solder to join these metals on the PCB. It is commonly made using tin and lead but due to hazardous concerns to the environment, most companies use lead-free solders to make the electrical bond.
If you are looking for a professional PCB design company then head on to this website pcbasic.com and avail the best high-quality PCB design and layout services.
Follow this article to read a complete soldering guide that includes some common materials used in the process and the different ways used in this process.
Materials Required for Soldering
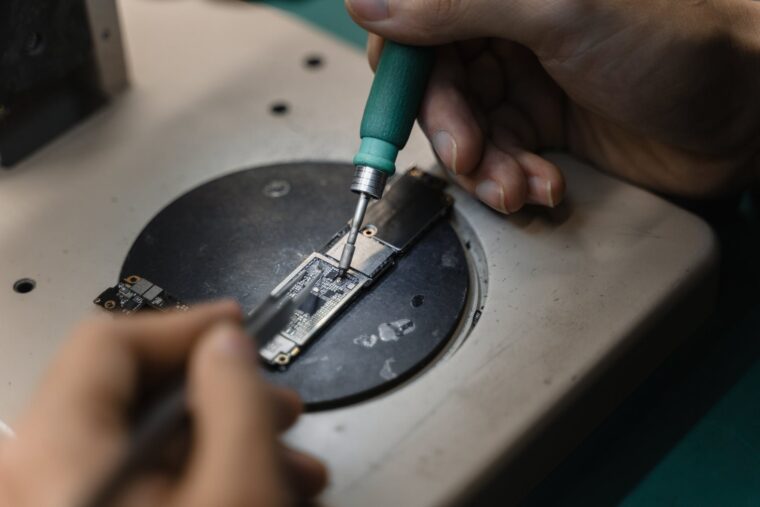
1. Flux
Flux is an important component while soldering plastic circuit boards and electronic equipment. It allows you to remove any oxide particles and avoids oxidation in metals. By preventing oxidation it enhances the soldering process and you can deliver good quality printed circuit boards to your customers.
There are different types of flux that can be used in this process. The main function of flux is to remove any oxide particles and other impurities from the copper wires on the circuit board. The different types of flux are used for different purposes based on the number of oxide particles you want to remove.
2. Solder
Solder is the primary material used for soldering. The life and performance of electronic equipment is based on the quality of printed circuit boards. If you want to manufacture a high-quality PCB assembly then ensure that you are using pure high-quality solder. Eutectic solder is best for soldering and you must melt them at a temperature of 183°C.
These solder are available in different forms which are in the form of bar, paste, performs, balls and wires. Currently, almost every company is using this new lead-free solder which has no hazardous components that can affect the environment and life on earth.
3. Electronic components required for soldering
Electronic components required for soldering are mainly divided into two different categories i.e., active and passive electronic components. Active components are the ones that have directionality during the technique. For example – Integrated Circuits, Logic gates, transistors etc.
Whereas passive electronic components don’t have directionality in the process. For example- capacitors, inductors, resistors and diodes. These electrical components are an important part of soldering without which the process will be incomplete. Ensure that the equipment is working fine before you start working.
Different ways of Soldering
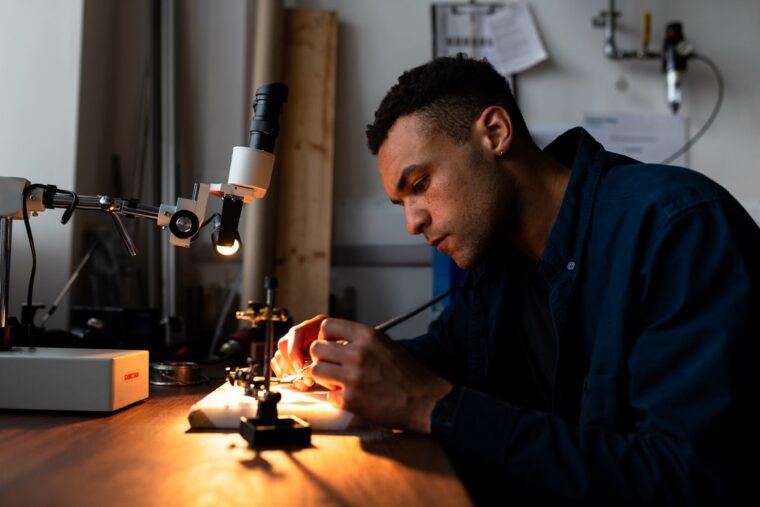
If you are planning to go into the PCB manufacturing business then ensure that you know the different ways to get the job done.
1. Wave Soldering
This is a basic soldering technique used by most manufacturers for mass manufacturing printed circuit boards. You will require the electronic components and basic raw materials for this process. Ensure that you are ready with all the equipment before you start the process.
There are different types of machines that can be used in this form ideal for both lead and lead-free wave soldering. Any type of machine used in this technique will work in the same mechanism and will deliver the same quality of output.
The raw materials used in this process includes – a wave soldering machine, flux, dip tester, solder bar reflow checkers, spray fluxers and flux controller. This technique takes place in three different stages. At first, it starts with the preheating stage where the PCB is preheated. Up next comes the fluxing stage where the flux is sprayed on the PCB using spray fluxers and at last comes the soldering stage to solder PCB.
2. Hand Soldering
This technique is used by manufacturers for low-volume production. It is mainly used for repairs and rework of printed circuit boards. In this process, you need a lot of raw materials and electronic devices. The process is quite time-consuming which is why it is done on a small scale.
For thru-hole or (SMDs) surface mount devices and chips you can use a soldering station or iron. This process is usually done with hot air pencils or hot air remote blowers. This technique is more effective for thru-hole components and repairs and reworks of PCBs.
The equipment you need in this form includes – Soldering station, iron, wire, solder paste, balls, pot, flux, tweezers, hot air system, smoke absorbers, heating gun, static eliminators, pick-up tools, waist straps, magnifying lamps, flux pen and an overcoat pen.
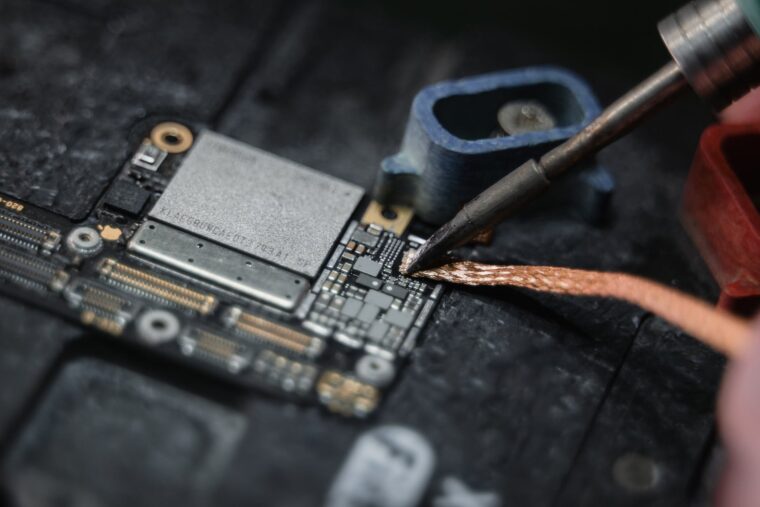
3. Reflow Soldering
This is another simple technique used in manufacturing companies for high-volume production. This process is also used for simple soldering surface mount devices and chips. You would require a reflow oven and checker, solder paste and flux. This technique doesn’t take much time and can be done without using many raw materials and electronic equipment.
This is an alternative and effective process to replace wave soldering and uses SMD technology. This process takes place in four different zones i.e., preheat, thermal soak, reflow and cooling. Once the circuit board passes all these four stages the process is completed.
The track of the circuit board is printed with solder paste applicable for both leaded and lead-free solder. With the help of a solder paste dispenser, you can print the solder paste throughout the process. Once the process is complete you can look for any defects, repair or rework.
4. Ball Grid Array (BGA)
This is another electronic form of manufacturing printed circuit boards. This is a modern technique nowadays used in most companies. You will require special components for this process and done with lead-free solder to deliver high-quality PCB assembly. This is another complicated technique that consumes a lot of time and is commonly used for repairs of electrical equipment.
The Bottom-line
This is the complete soldering guide that will help you to get a brief idea about how this process works and what materials you will need before you can start this process. The process is quite complicated and the performance of any electric device depends on this. Hence, ensure that you are not compromising on delivering the best output.