Plastic is one of the most useful and most used materials on planet Earth. Most people know why it is the most used material. It is because it is inexpensive, easy to manipulate and turn it into anything we want it to be. It is much easier to design a plastic part instead of something made out of aluminum, copper, stainless steel, or even stronger metals. Obviously, there are some downsides to using plastics, but do we/companies really have a choice? Manufacturing processes have to be as inexpensive as possible.
Everything needs to be optimized for the best cost-effectiveness otherwise a company cannot succeed and make profits. So, if you are just starting your business or have decided to cut down on manufacturing costs, you will probably need a little bit of help to design the plastic parts required for your product. To help you with that and ensure that all of your plastic parts are made with precision and with durability in mind, here are some tips I can share about the subject.
I hope that after reading through this article, you will manage to start properly designing and developing such parts.
Use the right type of plastic
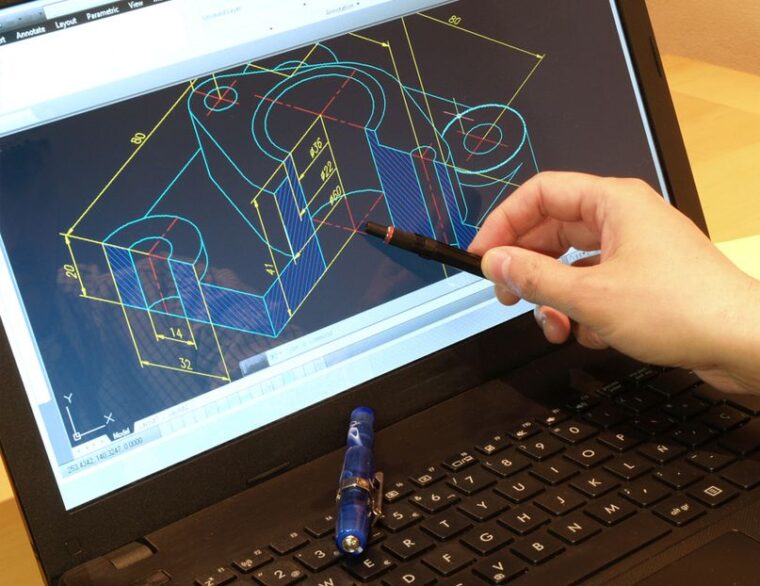
I mentioned different types of metal previously such as aluminum, copper, and steel. All metals, including those three, have different properties/specifications. One is more durable than the other. Another is higher on the Mohs scale of mineral hardness than another and so on. There are so many differences between these metals which is why we find different purposes for them.
For example, steel is used for construction while copper is used for wiring because it is better at conductivity.
The same applies to plastics. Yes, there are several different types available. You are probably asking yourself: Why is this important? Well, it is important because every single type has a different purpose. For example, one type of plastic can be used for regular bottles while on the other can be used for pipes or something else that requires a lot more durability.
In other words, depending on the part/product that you want to produce, you will need to pick the right polymer.
Here are some that you should probably consider:
- PA – Polymides – used for creating all kinds of durable fibers which you can usually find on a toothbrush, a fishing rod (the fishing line), inside of an engine, etc.
- PC – Polycarbonate – this one might be a little bit more durable because it is very flexible. Have you ever tried to break a CD or a DVD? Sometimes, they break, but it is very difficult because it is very flexible. That is because CDs and DVDs are made out of Polycarbonate. You can also find the use of PC in windows and glasses.
- ABS – Acrylonitrile butadiene styrene – Inexpensive and very commonly used as a casing for electronic parts. Most keyboards, monitors, and other PC peripherals are made with ABS. ABS is definitely something you should consider.
- PVC – Polyvinyl chloride – another one you should consider is PVC. Today, it is most commonly used for piping in the bathroom or in the walls because it is a great insulator. That is probably the reason why we use it for electrical insulation and even whether insulation. PVC is used for window frames too.
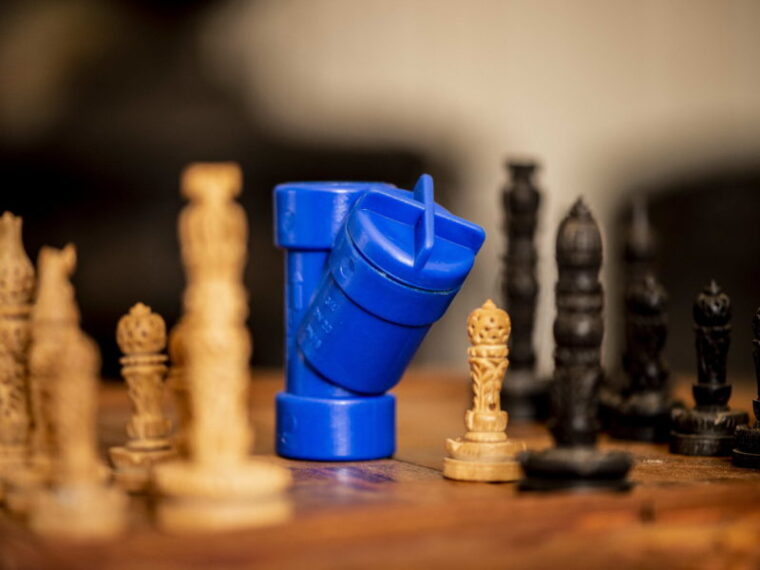
There are dozens more I could list, but I think these polymers are the most popular ones and most commonly used ones. Whichever one of these you pick, I am sure that most molding companies such as qmolding.com will be willing to manufacture your plastic part no matter which polymer you choose to use.
Make sure your design is precise
Whenever you create a design for smaller plastic parts, you have to ensure that everything is done correctly. The molding company will not be able to fix those mistakes for you. They cannot know what you have in mind. Of course, if certain things in your design are impossible to realize, they will inform you of that.
However, if you want a product that will have proper structural integrity, you have to ensure that every single measurement in your design is as precise as possible. Otherwise, you might end up with a week part that could easily break or get damaged in the future.
Be careful with the wall thickness
When talking about certain measurements in your design, I think you should pay extra attention to the wall thickness of the plastic. I had to mention this because a lot of people make this mistake regularly. By reducing the wall thickness, you get to save a lot of money, but you might also pass that threshold which makes your product much weaker.
It is also very important to make the wall thickness even. Because if it is uneven, there is an increased chance of problems with that part.
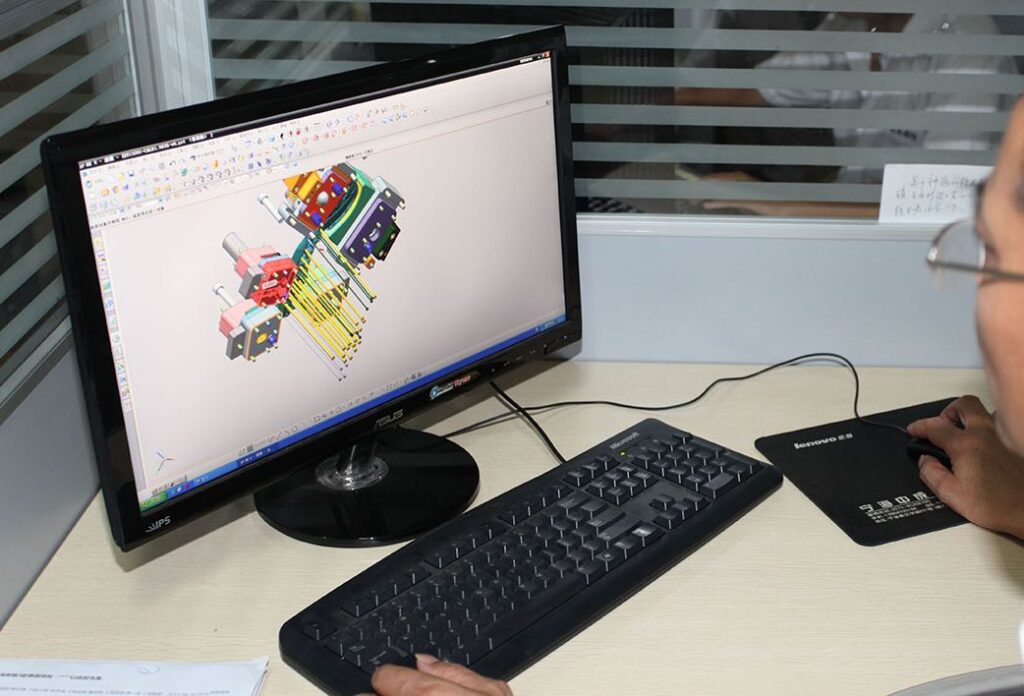
Forget about sharp or hard corners
As you probably already know, almost all plastic parts are made with injection molding. The melted polymer is injected into a mold with very high pressure. This high pressure allows the plastic to enter every single nook and cranny of the mold.
However, this process can never be perfect. Sometimes, not every corner of the mold will be filled. But, problems arise more commonly when the design of the mold (the part) has sharper and harder corners. Even with the high-pressure injection, the plumber has a harder time feeling in those sharper corners. So, if you want to reduce the chances of failure during the manufacturing process and if you want to save yourself a bit of money, I would recommend making your part with rounded corners.
I know, this kind of change might seem difficult or impossible to make, but once you consider how much money you could save, I think it is worth it. I even believe that the injection molding company will also inform you of this.
As you can see, there are very common mistakes you can make when designing plastic parts, but after reading through this article, I believe that you will not run into any complicated problem.