Delivering supplies, fulfilling contracts, and other concerns that our warehouse may have will happen upon a similar point of concern. That point being piece picking that’s employed for our business. Piece picking itself is a process of picking orders and grouping them within their designated containers.
This process is very important for warehouses and takes up a lot of its actual operational procedure. Not only that, the methods in which we may commit the picking within our warehouse can be crucial to the proper execution of our job. For the sake of keeping you in the know, here are some of the most popular picking methods along with their strengths and weaknesses.
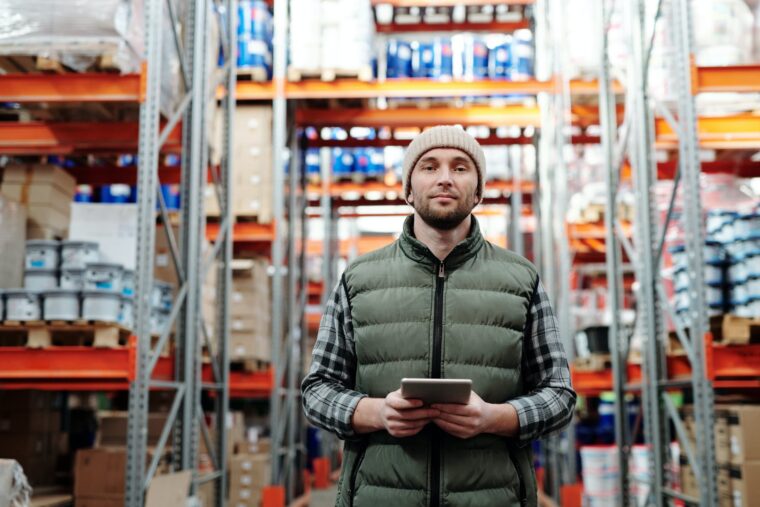
Single order picking method
The most basic picking method is single picking, also known as the basic picking, method. When applying this method, the picker will take one order at a time. The method has the picker visit every aisle until the order has been completed. However, this takes a lot of time due to the need to do so many visits to different aisles.
This picking method is not optimal for those who require speed or tons of orders to be processed daily. One shouldn’t use single order picking if they frequently get large orders. On the other hand, the smaller operations can get a whole lot of mileage out of this simple picking mechanism. The more specific and customizable aspects of the piece picking process are something you should check when purchasing and looking into parts.
Zone picking
If we wish to reduce the overall time it will take our picking system to complete an order we can divide our picking area into multiple zones with their own pickers. By doing this, we reduce the overall time each picker will take as well as the overall time we’ll need to get the necessary parts from each zone.
This method is called the zone picking method. When applying this method it’s important to know that pickers aren’t allowed to pick items from other zones at all. Due to this aspect of the method, orders are made to move between zones, acquiring items located within the zone before continuing onto the next one. With this style of picking, we can organize a path for each order to proceed through and even automatize a part of the process through the use of certain moving systems.
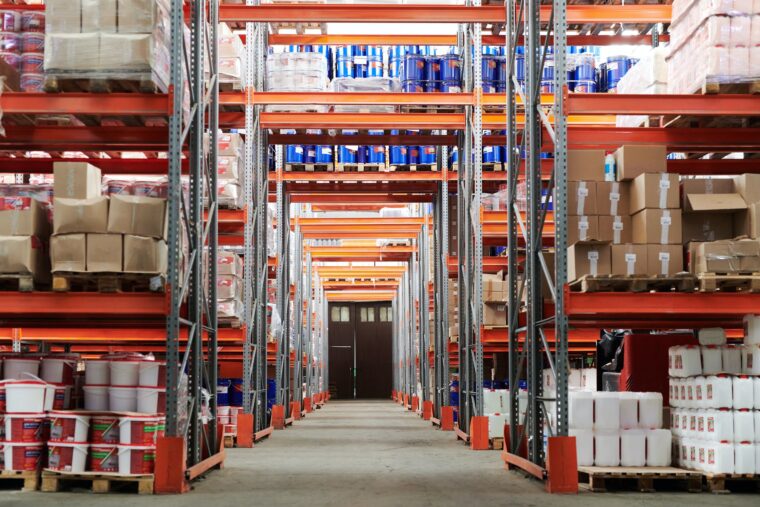
Batch picking
Going back to methods that rely on specific picker behavior rather than the area they are picking from, we have a batch picking system. This system allows the picker to pick up multiple orders at the same time by grouping the orders. By using this method, we can reduce the travel time by bringing over multiple items at once thus making the picker take fewer cycles to get all the items together.
However, the batch method doesn’t have the inherent ability to separate picked items. The drawback of this is that the orders could be mixed up and wrong orders could be assembled. If you apply this method it’s suggested you enhance the management of your orders so the mistakes happen less often, it will also allow you to resolve mixed orders before they are properly sent away. For more information on batch processing, visit https://www.jamsscheduler.com/solutions/batch-processing/.
Wave picking
The next picking method is wave picking. When using wave picking we group multiple orders together, each of these groups is called a wave. From there on, pickers pick items from each wave. However, this cannot be done without some additional preparation. The whole wave has to undergo a consolidation process that the pickers will create a list from. If it’s done incorrectly you’ll run into a lot of technical difficulties.
Wave picking also has a scheduling window that requires some orders to be scheduled to be picked up during certain times in order to properly coordinate the whole process and not run into clashing interactions.
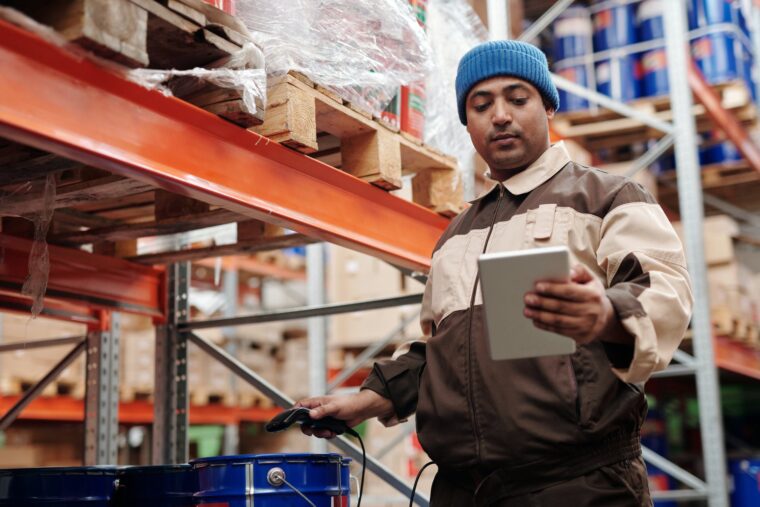
Mixed methods
While each method discussed above has its own strengths and weaknesses, we are also allowed to mix and match them together for better results and performance. When it comes to coupling methods into one, some of the most popular choices are zone-batch picking and zone-wave combinations.
The zone-batch combination allows us to assign each picker a zone while also giving them the added number of items that are picked up each trip by employing the technique of picking up multiple items that batch picking provides. That way, we can achieve pretty decent speed while cutting down orders with a lot of items to them.
On the other hand, the zone-wave combination is one of excelling management. It allows us to reduce the overall working area of each picker through the zone method while also providing the benefits of the wave picking method where the groups within each zone will be turned into waves for easier relocation. Of course, the potential issue of mixing up orders exists but considering scheduling is an important aspect of wave methods it translates here too while also being easier to manage due to zones having their own schedules.
These two methods aren’t the only combinations. In fact, there’s another option decently popular option. This method employs a combination of three other methods, making it way more complex but also extremely potent. This method is called the zone-batch-wave method.
Zone-batch-wave
When it comes to complexity, the zone-batch-wave method is the most complex combination method out of the available ones. It employs the combination of the three simpler methods to accomplish a lot better picking result.
The implementation leaves our pickers operating within a certain zone and picks items within the zone itself. The batch part comes in with the fact our picker will be picking up multiple items at once rather than a single one and thus allow our zones to be cleared faster. On top of it all, we add the wave methods grouping and scheduling functionality which assists in further optimizing the process.