A hydraulic power pack unit is a device containing three things mainly that is the motor, a fluid reservoir, and a pump. It runs on the principles of hydraulic power mechanism and is used to provide g power to motors, cylinders, rotary parts, or fans.
The working mechanism of a hydraulic power pack unit
The hydraulic power mechanism of the unit transfers the hydraulic energy of fluid within the system from one energy source to another. This helps get various types of motion such as the rotary motion of fans and motors, linear motion, or even force to a machine or industrial equipment.
An example of a hydraulic power unit would be the gas-powered hydraulic power unit, which you can check here.
Within the hydraulic power, the unit is a multi-stage pressurization process within the networks that forces the fluid with some energy. The system also incorporates temperature control devices that maintain the temperature inside the system to ensure the hydraulic fluid is not lost due to excessive heat and subsequent vapor loss.
Loss of hydraulic fluid in a system can cause a loss in desired pressure needed to run the industrial equipment, and reduce its operating efficiency and even render the system useless.
There are certain types of hydraulic power units and each one has certain mechanical specifications in it that allow them to be deemed fit for certain industrial processes.
For example, the ideal use for a gas-powered hydraulic power unit is to provide longevity to the motor and increase fuel efficiency.
Certain factors determine the performance factors of a hydraulic power pack unit. This is determined by the pressure limits during the use, the powering capacity based on which it can produce a certain amount of power needed to run a device, and the volume of the reservoir containing the hydraulic fluid.
There are some physical characteristics too that come in handy while buying one of these devices. You will have to look at the size of the hydraulic power unit, the power supply needed to run the device, and the pumping capacity along with the strength.
It is always a good idea to know about the basic components of a hydraulic power pack unit and then find out the components and their use.
Components necessary in the design of a hydraulic power pack unit
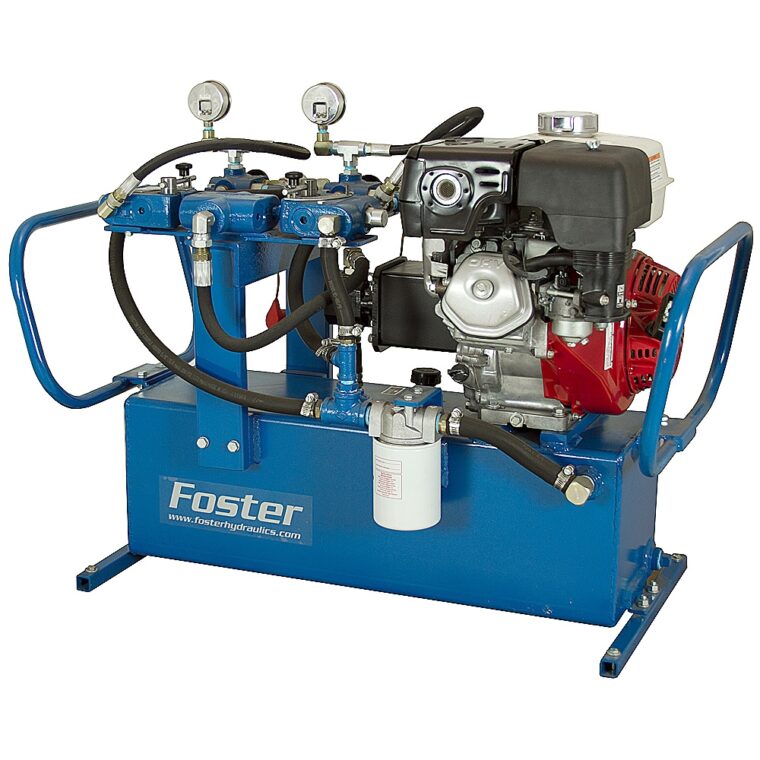
Some of the components that you find in all types of hydraulic power pack units including gas-powered hydraulic power units are given below for your reference:
Accumulators
The accumulators are cylinders that are attached to the hydraulic actuators. These collect the water from the pumps and store them that is necessary to build and maintain a certain amount of fluid pressure and supplement the motors.
Motor pumps
A motor pump is a critical component of the hydraulic power pack unit that has already been mentioned to you above. Sometimes systems may need more than one motor pump in them but usually only one of them would run at a time.
Tanks
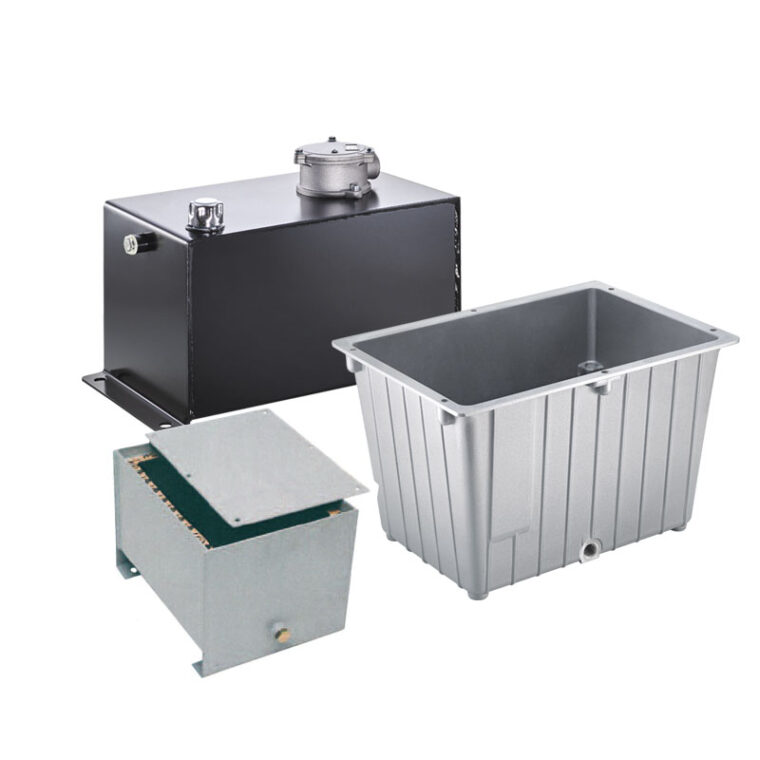
The tank is used for storing the hydraulic fluid that drains from the pipes. It can also sometimes store the actuator fluid coming out from the pipes.
Filters
A filter within the hydraulic power pack unit is a self-sustaining device that also has its motors, pumps, and of course a filtering device. It is a bypass unit that is installed on the top of the tank.
It has a bidirectional valve in it that can be used for filling or emptying the tank. As it is a self-sustaining device it can be replaced with a new one even when the gas-powered hydraulic power units are running.
Coolers and heaters
A cooling and heating system is necessary to monitor the temperature of the hydraulic power packs. It is highly important to keep the hydraulic fluid at the optimum working temperature when the power packs are running.
A cooling system such as a fluid or an air cooler can be installed behind the filtering unit to prevent overheating of the hydraulic fluid the pump during extremely hot conditions.
On the other hand, a heater is necessary for also the same reason but during the winter and extremely cool conditions to prevent eh hydraulic fluid from freezing inside.
Power unit controllers
It is the controller unit of gas-powered hydraulic power units that can be used for displaying and monitoring all the important features.
Hydraulic power pack units operation process
When you turn on your gas-powered hydraulic power units the gear pump takes out hydraulic fluid out o the tank and into the accumulator.
This process is ongoing till the time the desired amount of pressure is reached which is predetermined and preset.
A charging valve begins the pumping action of the fluid and the flow of the hydraulic fluid begins in the system.
There is a special one-way valve in the device that prevents the backflow of the hydraulic fluid to the accumulator.
But if the hydraulic pressure drops the charging valve would reactive itself allowing the accumulator to be filled with the desired level of the fluid again. When the fluid system begins to overheat which can be seen on the monitoring devices attached to the gas-powered hydraulic power units there is a temperature switch that shuts off the motor and prevents its damage due to overheating.
Here you got to know that having a hydraulic power pack unit that has multiple power units fitted to the system it is beneficial to turn off one pump and then turn on the other to keep the hydraulic power pack running efficiently without loss on output energy or power.
Having more than one pump in the hydraulic power pump can enable the system to run round the clock with efficient temperature control, fluid loss, etc.
Choosing your hydraulic power motors
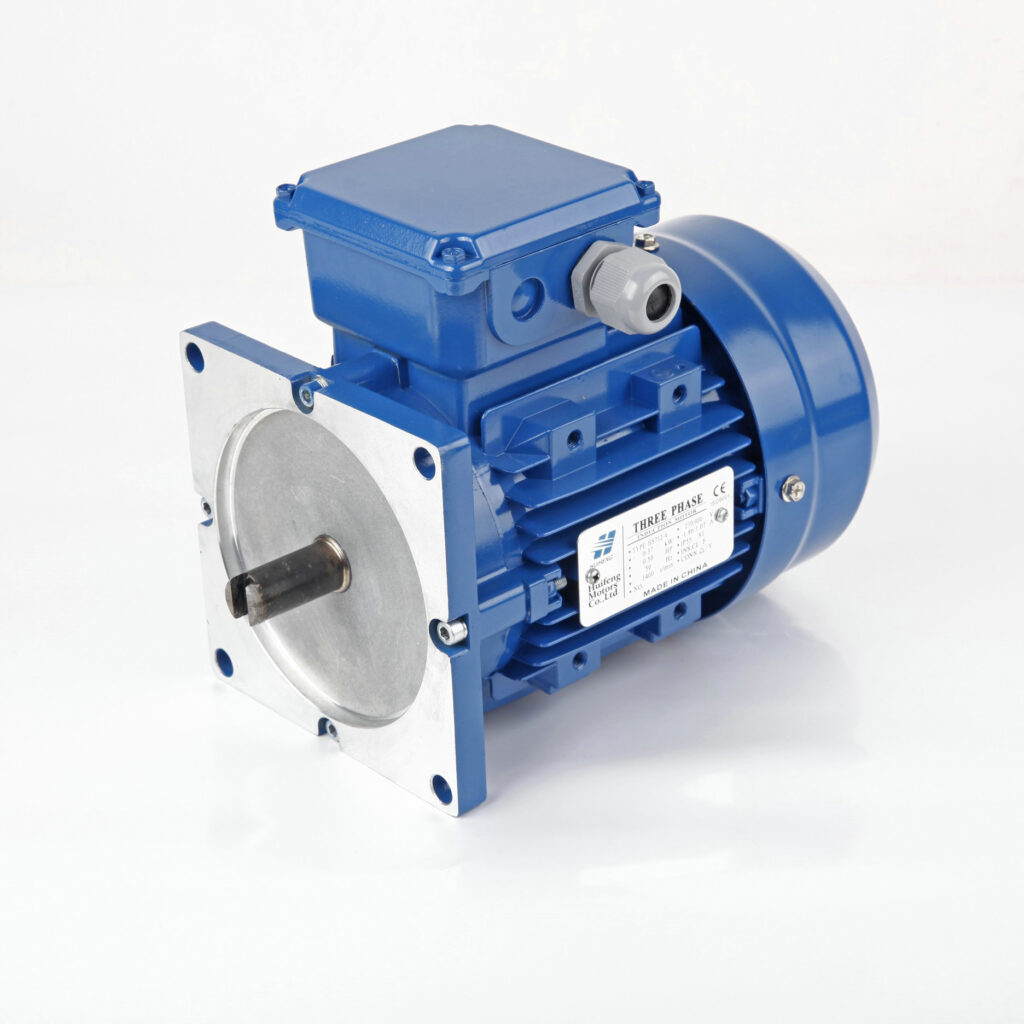
When it comes to choosing your hydraulic power pack unit certain things have to be kept in mind.
These include:
- Size of the motor or the input power type for the motor.
- Based on what type of power is needed to run the motor there are again two different types of motors.
These are:
- Electrically powered motors
- Gasoline or diesel-powered motors