Aluminum and epoxy composite materials are widely used in a lot of industries because of their ability to be customized, strength, and relatively low cost.
Epoxy resin aluminum can also be a great way to strengthen structures or hulls on boats or ships.
However, some epoxy resin aluminum projects will experience problems due to the inherent properties of the material. Below is a list of 10 common problems and how they can be fixed by those knowledgeable about this type of work.
You can also learn more about epoxy resin here: https://www.epoxyresin.biz/
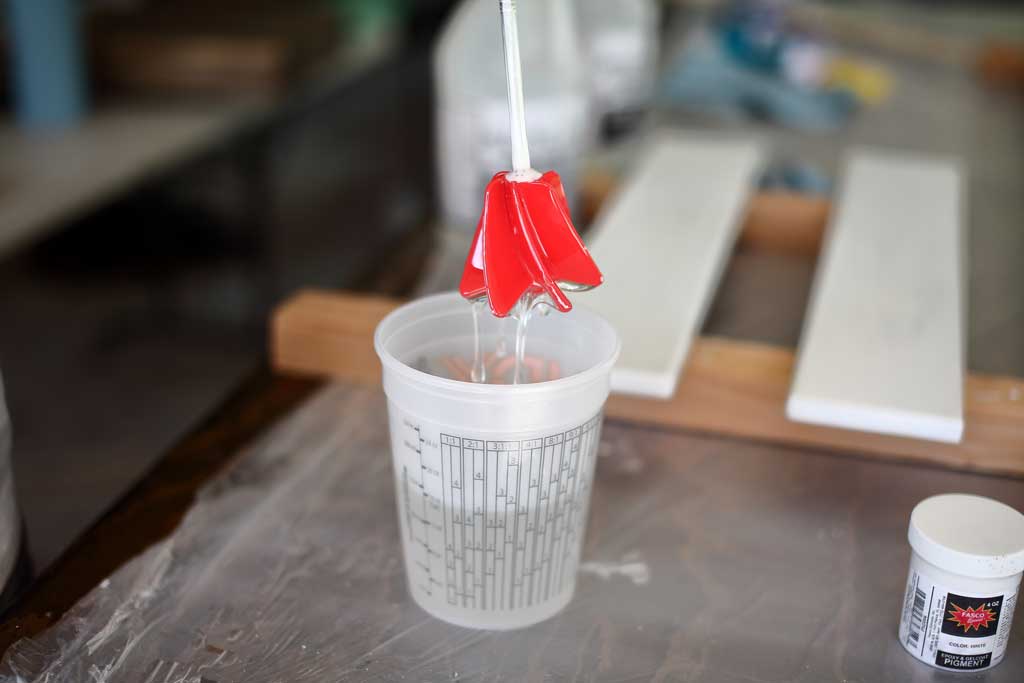
-
Blistering
This is a common problem and is usually caused by improper mixing of the epoxy, or sometimes it can be caused by too much heat in one area, causing the epoxy to cook. To fix this kind of blistering, try applying more heat to the part that is blistering to make the chemical reaction even out. If you can’t fix the issue that way, it may be best to reapply a fresh layer of epoxy resin over your existing thin layer.
Also, you may be able to avoid this problem by using a different epoxy.
-
Halos
This problem is caused by an epoxy resin reaction where you have not mixed your resin or hardener properly. The cure for this is to make sure your mix ratio of the resin and hardener is correct and to ensure that the part is getting enough heat and has time to cure before mixing with other layers.
Furthermore, if you find that you have haloing issues, it may be best to use a different epoxy resin.
-
Breaking in the middle
This problem is quite common with compression fittings or any type of fitting on boats or ships. Usually, this happens when there is water trapped inside the fitting, and then the pressure gets too high, causing it to break. To avoid this kind of issue in fittings, completely drain or purge any water from your fitting before pumping them up and sealing them off.
-
Tacky
This problem can be caused by under-curing, or sometimes it can be because you’re using a tackifier along with your epoxy resin. To fix this problem, try curing the resin for another few hours or longer, or try to find an alternative to the tackifier in your epoxy.
Additionally, if you’re using only epoxy resin, and it still is sticky, you may be using the wrong resin.
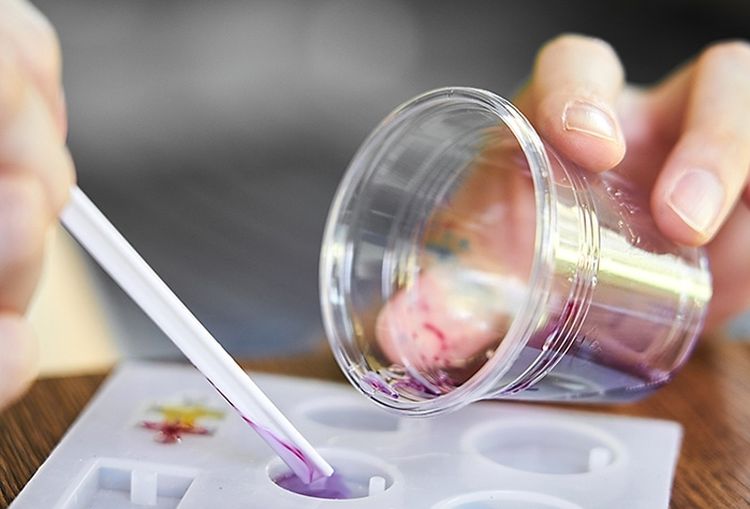
-
Incomplete Cure
This problem can be caused by environmental factors such as humidity and temperature. For a proper cure, you must ensure that the part is dry and has access to fresh air while it cures. If this is not possible, use a kiln or oven to dry out your epoxy resin before using it again.
Moreover, you should try to cure your resin in a contained environment such as a resin oven, which will accelerate the cure time and ensure that you have a fully cured piece.
-
Drying Out After Curing
This problem can be caused by not allowing your epoxy resin to dry out properly. The cure for this is to ensure that the resin is cured completely and allowed to dry for three days before using it again.
Also, if you notice some of your epoxy resin has a completely different color than the rest, that is usually because your gas cylinder or torch has been exposed to oxygen and has allowed this to happen in part.
-
Early Crack Growth
This kind of epoxy reaction can occur if you don’t use enough hardener in the mix or too much hardener is used. To fix this problem, find the proper ratio for your mix of epoxy resin and hardener, and ensure that the resin is properly cured.
Then, if your resin already has cracked, you may be able to sand down the layer around the damaged area to remove the damaged resin and then reapply another layer of epoxy over the top.
-
Discoloration
This can be caused by using too much heat or too much time in the car before curing. To fix this problem, make sure that you’ve cured your epoxy properly by drying it out for several days before working with it again.
Also, try to make sure that the resin is 100% dry before using it, as this can also lead to discoloration.
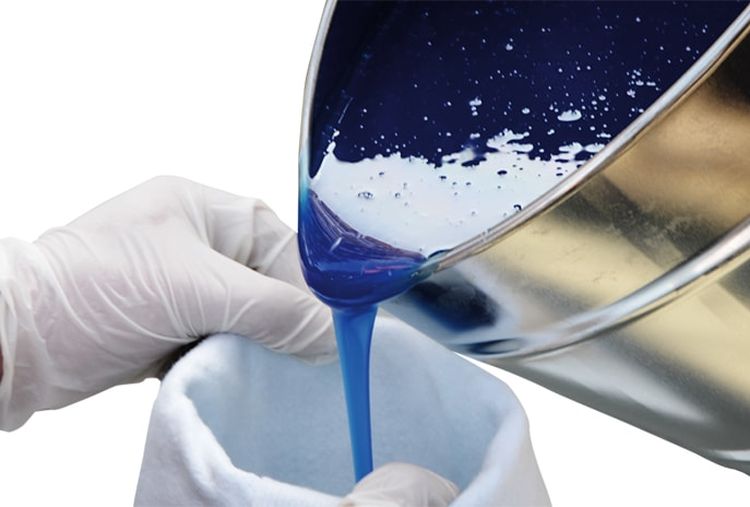
-
Haze/Clouding
This problem can be caused when the epoxy mix ratio is wrong, or sometimes it can be due to environmental factors such as temperature or humidity. To fix this problem, get the proper mix ratio correct for your epoxy resin, and then cure it properly so that there are no environmental factors affecting it.
Also, if you notice that your resin is cloudy, you can fix this problem by scraping the affected area with a razor blade.
-
Over Curing
This can be caused by the environment, or sometimes it can be caused by having too much heat when curing. To fix a layer that has over-cured, simply send it back down and apply another layer.
Moreover, if you notice that your epoxy resin has a different color than the rest, this is usually because your gas cylinder or torch has been exposed to oxygen. To prevent this, make sure you have a regulator on your torch and ensure that the material you’re working with is 100% dry.
-
Dimensional Changes
This sort of problem can occur due to improper mixing of the epoxy resin with the other additives or parts that are being secured together by the epoxy. The solution to this problem is to mix the resin thoroughly with all parts and use the right amount of hardener for your resin.
Also, you should make sure that the epoxy is cured completely before using it and avoid working with it when there is excessive heat present.
Every epoxy resin is different, and every batch of resin may be affected differently, so never ever assume that your headache will only last five days because if your gel inhibitor is the right choice for you, it may only last five days or a month. You better always keep in mind that Curing is an art, not a science. There are many things you can do to help speed the curing process, but the main thing is to allow it and yourself to cure properly without too much heat, as that will speed up the entire curing process.
Unfortunately, there is no exact timetable of how long your epoxy material will last. It can last a few days or a few months. It depends on what type of epoxy resin and hardener you use.