When it comes to choosing the right plastic mold maker, certain guidelines can help you make the right decision. What you don’t want to be doing is picking the wrong machine for the wrong mold.
But from the wide range of tips and tricks on how to prevent this costly mistake, there are a few that stand out from the rest. If you don’t want to miss the most important criteria that will cost you consistency and profits, then this is the guide for you.
In this article, we will talk about the 6 tips for choosing the right plastic mold maker. So, without further ado, let’s start.
1. Never Buy A Used Machine
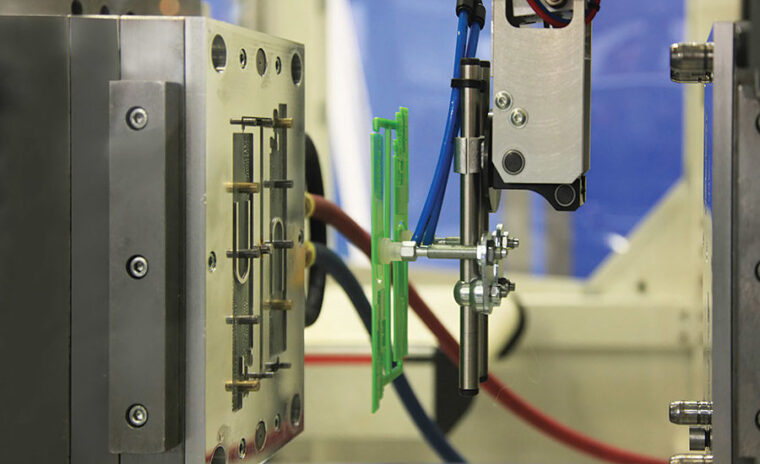
If you are buying a used molding machine, then chances are the machine either doesn’t work at all or there is something wrong with it.
In very few scenarios would a company or individual resell a molding machine. Since the industry is booming, there is no need for these individuals to put their molding machines for sale, so you need to think twice about it.
While there are obvious scenarios where someone would be selling such a machine, it’s important that you don’t repeat the mistake that many have done previously.
When looking to buy a machine that’s already been used, make sure that the particular unit is fully operational and has no issues plaguing it.
This can easily be done if you do a full inspection and test it before committing to buy the thing.
After a couple of tests, you will have a general understanding of the quality and whether it breaks down often or not.
2. Never Go For Large Screw Diameters
This is a costly mistake that many people do. When it comes to buying the perfect molding machine for your plastic molding needs, a large screw diameter will only cause trouble.
This is because large screw diameters have issues when it comes to material degradation. Material degradation happens more often when the material spends more time in the barrel. This is only possible if you are using large screw diameters.
3. Look For Other Types of Screws
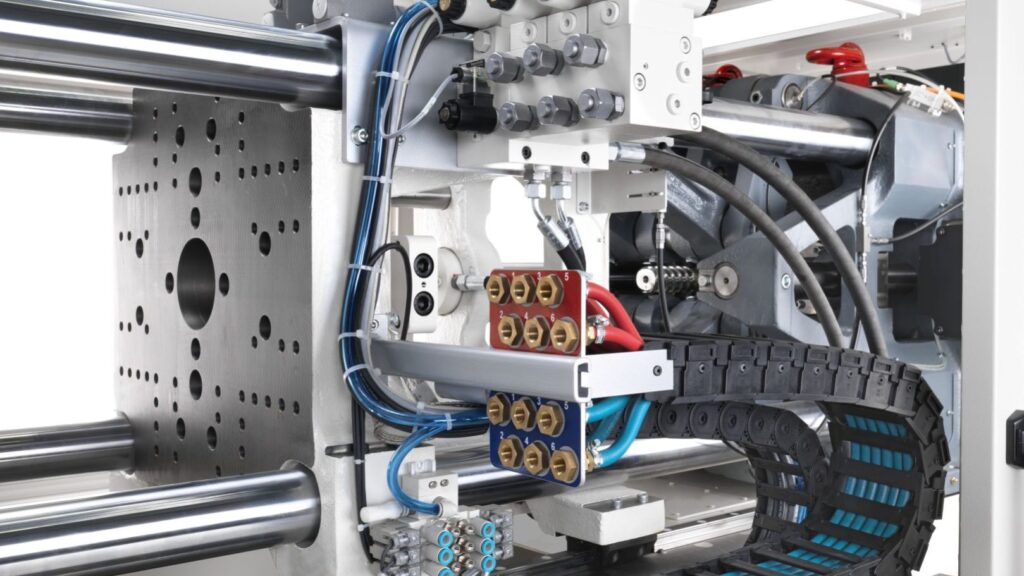
Large screws aren’t the only answer to this problem. Countless others do a better job for the type of molding you need.
One type of screws is general-purpose screws. These types of screws are heavily used with all kinds of plastic molding. Their use stems from their flexibility and moldability. General-purpose screws are used with PP, PE, Nylon, PC, and all other types of plastic.
This makes it one of the most popular types of screws used with plastic molding machines. However, these aren’t perfect and they have certain disadvantages.
One of the biggest disadvantages is the fact that some materials will see lower productivity rates compared to others. Screw selection is very important and you should spend some time researching the topic.
But there are also other things you can learn that can make the selection process easier. If you happened to be interested in which companies offer the best service, then make sure to visit Moldall.
4. Make Sure the Process Isn’t Limited
When it comes to mass production, you wouldn’t want the plastic molding process to be limited by anything. However, a lot of machines have an injection pressure limit that produces short moldings whenever the machine has insufficient pressure.
This is why it’s recommended that you always keep at least 10% of the pressure in reserve so that the machine can do its thing without harming productivity.
This is a crucial tip that everyone should pay attention to. If the particular machine doesn’t allow for pressure to be limited, then you will produce faulty parts.
Also, the pressure limit works in accordance with the screw diameter. So it’s safe to say that the pressure and type of screws go hand in hand.
5. Know What Type of Plastic You Need to Mold
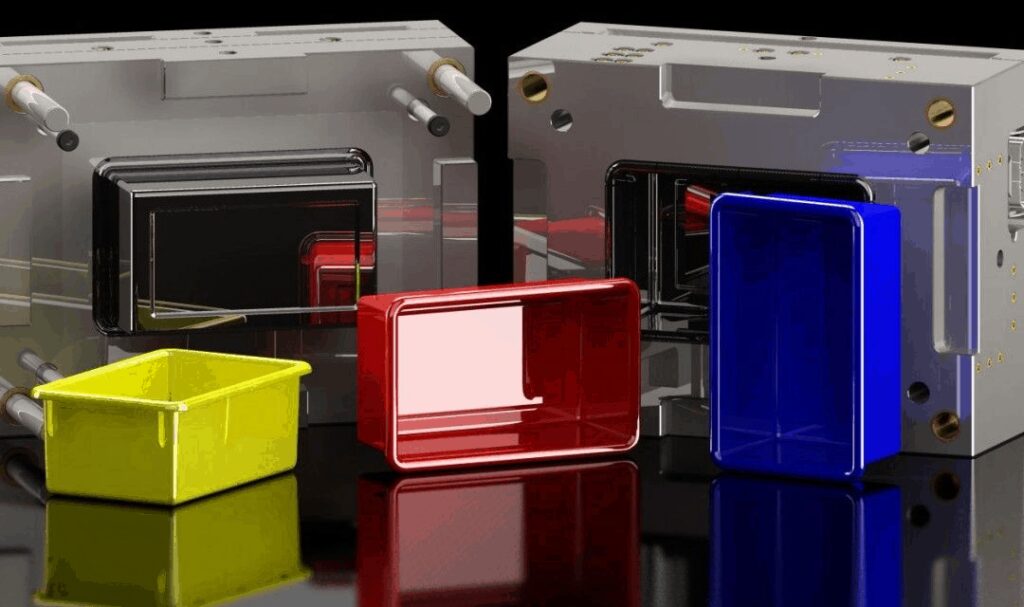
Now, let’s move onto tips that are more accustomed to your needs. So far we’ve discussed general tips about the machine itself, so let’s touch on material-specific tips.
The first one is to know the type of plastic part that you plan on molding. Is this part suited for the machine? Can it fit the mold size and weight? There are lots of things to go over when we talk about the type of plastic part.
Some of them are the material, weight, length, wall section, gate location, quality requirements, cycle time, and more.
6. Type of Machine
When it comes to the machine itself, there are three types that exist. The first one is the fully hydraulic, the fully electric, and the hybrid.
Let’s talk about them.
-
Fully Hydraulic
If you’re looking into buying a dully hydraulic machine, then you need to make sure the machine is right for your needs. For example, energy efficiency is an important factor, then a fully hydraulic machine is right for your needs.
Here are some other criteria that can help you decide in favor of this type of machine:
-
Great as new or as used
-
Least expensive option
-
Energy efficient
-
Processes plastic parts
-
Can design parts and molds
-
Easy serviceability
These are, among others, important criteria that you need to go over if you’re buying this machine.
-
Fully Electric
These types of machines offer quality repeatability which makes them some of the best when it comes to mass-producing. They are extremely accurate and quite often used in the medical industry.
More specifically, they are used in the making in the molding of medical devices.
-
Hybrid
The hybrid is the last option on this list and one that might be best suited for your needs. A hybrid is a combination of a hydraulic and an electric that can perform both types of drives.
These are generally faster when it comes to injection and molding. But the reason why they are so popular is the fact that they are extremely energy efficient and accurate.